Product packaging plays a vital role in protecting and preserving the quality of the product during transportation. Laminates provide an additional protective layer that shields against moisture, oxygen, light, and other contaminants. Moreover, they enhance the packaging’s aesthetic appeal, captivating consumers with its attractive design.
Packman Packaging India’s leading packaging printing company discusses a few of the commonly used types of laminates for packaging.
1. Gloss lamination is widely recognized for its high shine and reflective finish, which adds a touch of sophistication and attractiveness to packaging. It enhances color vibrancy, making packaging appear brighter and more vivid, ideal for conveying a youthful feel.
However, it can hinder text readability, and show fingerprints, and smudges. Lighter colors minimize fingerprint visibility. They are used for products such as cosmetics, chocolates, and luxury items.
2. Matte laminates are known for their non-glossy, velvety appearance that gives a sophisticated, understated effect to packaging. Matte laminates reduce glare, making them ideal for packaging that requires easy readability of text and minimal distraction from graphics. They also provide a luxurious feel and can convey a sense of exclusivity.
Matte lamination conceals imperfections, provides a tactile experience, and is ideal for recycled or durable custom packaging. However, the dull color can also affect the vibrancy of the images on the packaging. These laminates are commonly used for electronics, personal care products, and high-end stationery.
3. UV-resistant Gloss Laminate: This type of laminate combines the benefits of both glossy and matte finishes. It protects the packaging from fading and discoloration caused by exposure to ultraviolet (UV) light. It is applied selectively to specific areas of a package, creating a striking contrast.
It can enhance text, logos, or images, making them appear more vibrant and visually appealing, and also increases the longevity of the packaging materials. UV gloss laminates are commonly used for product labels, packaging for beverages and snacks, and promotional materials.
4. Satin laminates: Crafted with resilient polypropylene, our non-reflective satin coating offers a gentle aesthetic and safeguards ink against marks and abrasions. They offer a smooth, silky texture with a subtle sheen, striking a balance between gloss and matte finishes.
These laminates are often employed for packaging materials like food boxes, wine labels, and gift bags. Satin laminates provide a touch of sophistication and a tactile experience while minimizing reflections and fingerprints. They create a refined look suitable for products that seek a premium feel without the high gloss effect.
5. Aluminium foil laminate: Aluminium foil, commonly used in kitchen pantries, serves multiple purposes such as grilling, storing leftovers, and cleaning grill grates. It is food-safe, plastic-free, lightweight, and recyclable.
These laminates consist of a layer of aluminum foil combined with other materials like paper, plastic, or film. They offer effective barriers for packaging perishable food, pharmaceuticals, and sensitive products like coffee and tea.
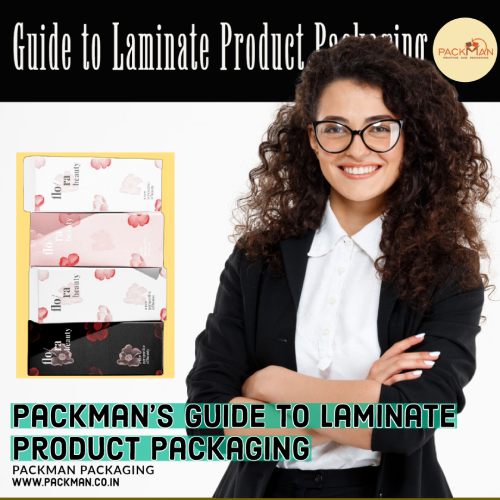
6. Metallized Laminates: Metallized laminates consist of a thin layer of metal, usually aluminum, deposited onto a substrate such as plastic film. They provide barrier properties, durability, and an attractive appearance.
Metalized laminates are used for packaging snacks, chocolates, and other products that require a premium look. However, it differs from Aluminium foil laminate in that while the Metallized laminates have a thin vapor-deposited metal layer on plastic film, aluminum foil laminates have a layer of aluminum foil between layers of film or paper.
Selecting the appropriate laminate for packaging is essential to create a visually appealing and functional product.